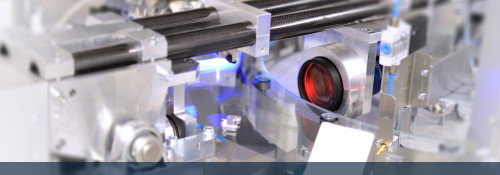
In automatischen optischen Mess-, Prüf- und Sortiermaschinen werden Güter und Komponenten visuell unter Einsatz von Bildverarbeitung geprüft.
Da in vielen Industriebereichen steigende Anforderungen an die qualitative Güte von Teilen gestellt werden, ist eine Automatisierung der Qualitätssicherung unerlässlich. Die herkömmliche Sichtprüfung in der Produktion mit dem menschlichen Auge stößt aufgrund der geforderten Durchsätze schnell an ihre Grenzen. Hohe Taktraten sowie die Forderung nach einer reproduzierbaren, objektiven 100% Prüfung fördern die Nachfrage nach automatisierten Systemen zur visuellen Prüfung - also einer automatischen Sichtprüfung. Außerdem wird die Dokumentation der Qualität immer wichtiger, ebenso das Ineinandergreifen bzw. Vernetzen aller Produktionsprozesse (Industrie 4.0).
Eine automatisierte optische Qualitätskontrolle ist heute aus vielen Produktionsprozessen nicht mehr wegzudenken. Vor allem für große Produktionslose, die schnell und zuverlässig auf Oberflächendefekte und/oder Maßhaltigkeit geprüft werden sollen, sind automatisierte Prüfysteme zur optischen Kontrolle unerlässlich. Die Vorteile dieser Art der optischen Prüfung liegen auf der Hand:
Ein optisches Inspektionssystem setzt sich üblicherweise zusammen aus Kamera/Optik, Beleuchtung, sowie einer Bildverarbeitungssoftware zur Auswertung der Aufnahmen. Dazu kommen ggf. mechanische Komponenten zur Positionierung der Prüflinge vor der Optik. Je nach Anwendung können die visuellen Inspektionssysteme in bestehende Produktionslinien integriert werden oder als individuelle Anlage Teile im vollautomatischen Durchlauf prüfen und sortieren. Gepaart mit den entsprechenden Zuführungs- und Verpackungseinheiten entstehen so Prüf- und Sortieranlagen zur Oberflächeninspektion, die genau auf die jeweiligen Anforderungen zugeschnitten sind.
Grundlage der optischen Sortierung ist die Bildaufnahme, welche die Basis für die Auswertung durch eine spezielle Software bildet. Die Qualität der Aufnahme oder, genauer gesagt, das Erreichen des bestmöglichen Kontrasts, ist entscheidend für die Qualität der gesamten Prüfung. Nur wenn ein Fehler sichtbar gemacht werden kann, kann er von der Software ausgewertet werden. Daher müssen die Komponenten der Bildaufnahme, d.h. Kamera, Objektiv und Beleuchtung, immer perfekt auf die Eigenschaften der Prüfobjekte abgestimmt sein. Die optimale Beleuchtung spielt eine große Rolle, oft werden hier mehrere Möglichkeiten ausprobiert, um den besten Kontrast zu erzielen. Beispielsweise können hier diffuse oder gerichtete Beleuchtungen, Hellfeld- oder Dunkelfeldanordnungen, bzw. Auflicht- oder Gegenlichtbeleuchtungen ausgewählt werden.
Da die Klassifizierung der Prüflinge quasi in Echtzeit erfolgen muss, d.h. im vollautomatischen Durchlauf, kommt sowohl den Hardwarekomponenten als auch der Bildauswertungssoftware eine besondere Bedeutung zu. Hier gilt, je leistungsfähiger Hardware und Algorithmen sind, desto komplexere Prüfaufgaben bzw. höhere Durchsätze kann das AOI-System realisieren.
Ein immer wiederkehrendes Thema bei der optischen Oberflächenkontrolle bzw. Vermessung ist der so-genannte Pseudoausschuss. Hierbei handelt es sich um geprüfte Teile, die vom Algorithmus des Prüfsystems als fehlerhaft eingestuft wurden, obwohl sie es tatsächlich nicht sind.
Die Gründe hierfür sind vielfältig, es können z.B. Veränderungen am Material, des Produktionsprozesses oder der Umgebungsbedingungen vorliegen, die eine Neukalibrierung des Prüfsystems oder die Anpassung der Prüfprogramme erfordern. Die in den Prüf- und Messsystemen von NELA eingesetzten Sensoreinheiten und unsere hausintern kontinuierlich weiter entwickelte VisionCheck Auswertungssoftware bieten vielfältige Adaptionsmöglichkeiten, um Pseudoausschuss zu verringern bzw. zu vermeiden.
Das Produktprogramm von NELA für die automatische Inspektion deckt eine hohe Varianz an Prüfanforderungen ab. Dabei sind unsere Systeme gleichermaßen für optische Oberflächenprüfungen wie auch für die Vermessung geeignet. NELA Prüfstationen gibt es in verschiedenen Ausführungen, z.B. als Glastellersystem, Bandsystem, oder getaktetes System. Je nach Anwendung, Form & Größe bzw. Materialeigenschaften Ihrer Serienteile bieten wir Ihnen das jeweils passende Inspektionssystem an.
Glasteller Prüfsysteme eignen sich für die vollautomatische und zerstörungsfreie Maßhaltigkeitsprüfung, Defektinspektion und Sortierung von Serienteilen für unterschiedliche Anwendungen. Sie kommen als optische Sortieranlagen insbesondere bei hohen Prüfanforderungen zum Einsatz, da durch die Glasteller eine hohe Stabilität des gesamten Prüfprozesses, insbesondere bei der Geometrieprüfung, gewährleistet ist.
Bandbasierte Prüfsysteme eignen sich insbesondere für die Inspektion von Kleinst-teilen bzw. von Teilen mit einem instabilen Stand, die aufgrund eines ungünstigen Höhen/Breiten-Verhältnisses nicht auf einem Glasteller geprüft werden können. Bandsysteme sind ebenfalls ideal für Teile, bei welchen vorrangig auf Oberflächenfehler geprüft werden soll. Dabei können die Prüflinge für eine vollständige, allseitige Prüfung auch gewendet werden.
Unter getakteten Systemen versteht man Werkstückumlaufsysteme, welche die Prüfteile individuell vor einem oder mehreren Sensoren positionieren. Diese Systeme sind für komplexe Teile bzw. sehr hohe Prüfanforderungen konzipiert, es können sowohl Geometrie- als auch Oberflächenfehler detektiert werden. Elastische Teile, wie z.B. Dichtungen aus Gummi- oder Kautschukmischungen, können zum Auffinden verborgener Defekte gedehnt oder gequetscht werden.
In Branchen wie z.B. in der Automobilindustrie und in der Medizintechnik gibt es häufig sehr hohe Anforderung an die Qualität von technischen Komponenten, oft gepaart mit einer Null-Fehler-Vorgabe. Die AOI-Systeme von NELA sind so universell ausgelegt, dass sie sich für die Sichtkontrolle von unterschiedlichsten Serienteilen eignen, die in verschiedenen Branchen zum Einsatz kommen. Ob Dreh- und Frästeile, Verbindungselemente oder Komponenten aus Kunststoff und Kautschuk, NELA Prüfstationen kommen bei einer Vielzahl von Prüfaufgaben zum Einsatz.
Welches Prüfsystem zur visuellen Prüfung für Ihre Branche bzw. Anwendung infrage kommt, hängt von individuellen Faktoren wie Materialbeschaffenheit, Form und Größe ab, sowie von den Prüfanforderungen. Unser Vertriebsteam und unsere Applikation beraten Sie gerne und erstellen ggf. eine Machbarkeitsstudie.
Auch wenn Prozesse wie CNC-Fräsen, Drehen usw. als sicher und präzise gelten, können Qualitätsschwankungen aufgrund von Fehlfunktionen, Variationen im Rohmaterial oder der Handhabung auftreten. Mit einem Inspektions- und Sortiersystem von NELA in Ihre Produktion integriert können Sie sicher sein, dass alle Teile, die von dem System als "Gut" klassifiziert wurden, die höchsten Qualitätsansprüche erfüllen: Ihre Ansprüche.
Präzisions- und Mikropräzisionsdrehteile können alleine aufgrund verschiedener Drehverfahren in Form, Größe und Oberflächenbeschaffenheit stark variieren. Komplexe Geometrien und enge Toleranzen bei der Maßhaltigkeit stellen besondere Herausforderungen an die Qualitätsprüfung. Die automatischen optischen Inspektionssysteme von NELA werden anwendungsbezogen hinsichtlich Material, Oberfläche, Form, Größe und Defektkatalog eingerichtet und mit den entsprechenden Zuführungs-, Absortierungs, Kamera- und Beleuchtungskomponenten ausgestattet.
Neben der dimensionalen Prüfung und Höhenprüfung werden die Prüflinge auch auf eine zuverlässige Funktionserbringung, z.B. auf fehlerfreie Oberflächen an Funktions- und Dichtflächen, kontrolliert.
Bei der optischen Inspektion von Verbindungselementen und Umformteilen ist die vollumfängliche visuelle Oberflächenprüfung, einschließlich einer Gewindeprüfung, eine herausfordernde Prüfaufgabe. Mit unseren speziell für diese Anwendungen konzipierten Inside und Outside Sensoren sind wir in der Lage, jeden einzelnen Mikrometer der Bauteiloberfläche, inklusive des Gewindes nach Defekten zu inspizieren. Zusätzlich erfolgt eine hochpräzise Maßhaltigkeitsprüfung, und die geprüften Teile können nach kundenspezifisch konfigurierbaren Kriterien sortiert werden. NELA Prüf- und Sortiersysteme sind für ein breites Spektrum an Kalt- und Warmumformteilen, Elementen der Verbindungstechnik (u. a. Nieten, Muttern, Schrauben und Verbindungselementen), Buchsen, Hülsen und Scheiben geeignet!
Die hochpräzise Inspektion wesentlicher Konturmerkmale und eine Maßhaltigkeitsprüfung Ihrer Sinterteile ist entscheidend für die Erreichung einer hohen Kundenzufriedenheit und -bindung. Unsere hochpräzisen Lösungen in standardisierten Inspektionssystemen, aber auch für individuell an die Kundenbedürfnisse ausgerichtete Prüfmaschinen, stellen die Überprüfung der häufig nachbearbeiten Sinterteilaußenflächen auf topologische Beschädigungen (Kantenausbrüche, Ausblühungen, Risse und Lunker) sicher und detektieren Schleifmittelrückstände.
Die präzise Überprüfung von Maßhaltigkeit und Geometrie Ihrer Stanz- und Feinschneidteile, unter Berücksichtigung der Schnittgrathöhe und des Stanzeinzugs, ist für die Erreichung Ihrer Qualitätsvorgaben entscheidend. Die automatisierten Mess-, Prüf- und Sortierlösungen von NELA stellen eine umfassende Geometrieprüfung Ihrer Teile sicher. So garantieren unsere Inspektionssysteme eine präzise Maßhaltigkeitsprüfung und sichere Ebenheitsinspektion Ihrer Blecherzeugnisse.
Um höchste Kundenzufriedenheit zu gewährleisten, müssen Hersteller von hochqualitativen Kunststoff- oder Kautschukteilen, wie z.B. Dichtungen, absolut sicher sein, dass alle gelieferten Teile die Qualitätsvorgaben erfüllen - ohne Abweichung. NELA Prüf- und Sortiersysteme sorgen durch eine berührungslose optische Inspektion mit hohem Durchsatz dafür, dass jedes Teile Ihre Fertigung zeitgerecht und einwandfrei verlässt. Durch eine vollständige Prüfung der Oberfläche sowie Maßhaltigkeitsprüfung im Mikrometerbereich werden dabei selbst höchste Industriestandards erfüllt. Durch Quetschung und/oder Dehnung elastischer Teile können selbst verborgene Defekte wie z.B. Risse entdeckt werden.
Bei der Entwicklung erneuerbarer Energien wird der Wasserstoff künftig eine große Rolle einnehmen, wobei der Speicherung des Wasserstoffs als Energiequelle und dessen Umwandlung in elektrische Energie eine besondere Bedeutung zukommt. Die in der Wasserstoff-Technologie eingesetzten Bipolarplatten erfüllen wichtige Funktionen innerhalb der Brennstoffzellen, denn sie
Bipolarplatten sind also ein integraler Bestandteil von Wasserstoff-Brennstoffzellen, sie sind jedoch im Herstellungs- und Verarbeitungsprozess anfällig für Beschädigungen und Defekte, welche sich auf die Wirkung der Platten z.B. als Dichtung oder Leiter auswirken können. Es ist daher essentiell, diese Fehler und Beschädigungen frühestmöglich festzustellen, dazu gehören u.a. Verformungen, Oxidation, Fremdpartikel, Luftblasen.
NELA Mess- und Prüfsysteme können die für die Funktion der Platten wichtigen Eigenschaften überprüfen und die entsprechenden Defekte auffinden. Da Bipolarplatten hoch spiegelnd sind, was für die Defektinspektion eine Herausforderung darstellt, wird die Shape-from-Shading Technologie eingesetzt. Entsprechende Sensoren werden in die Prüfstationen integriert und softwareseitig eingebunden.
NELA ist Mitglied des Cluster Brennstoffzelle BW, welches die Weiterentwicklung der Wasserstoff-Technologie zur Serienreife vorantreibt. Weitere Infos: https://www.e-mobilbw.de/netzwerke/cluster-brennstoffzelle