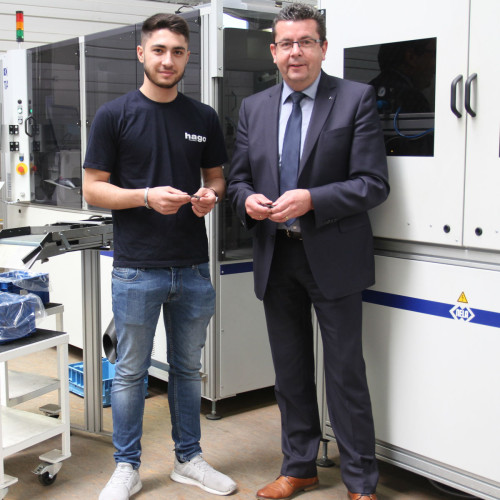
Der im südbadischen Küssaberg ansässige Blechteilespezialist HAGO Feinwerktechnik GmbH setzt in der Qualitätssicherung seit Herbst 2016 auf ein voll automatisiertes Prüf- und Sortiersystem der Firma NELA. Dabei werden die verschiedenen Prüfteile nicht nur einer hochpräzisen Maßhaltigkeitsprüfung, sondern auch einer Defektinspektion von allen Seiten unterzogen.
Bevor der Hersteller hochwertiger Stanzteile für die Automobilindustrie, die größtenteils im Feinschnittverfahren gefertigt werden, auf NELA aufmerksam wurde, gab es neben der automatischen Maßhaltigkeitsprüfung eine visuelle Sichtkontrolle der Bauteile hinsichtlich Oberflächenfehlern durch geschulte Mitarbeiter. Steigende Qualitätsanforderungen und wachsende Produktionslose führten jedoch zu einem Überdenken des gesamten Qualitätssicherungsprozesses.
Hier kam die Firma NELA Brüder Neumeister GmbH aus Lahr ins Spiel, die sich zuvor bereits als Lieferant hochpräziser, kundenspezifischer optischer Prüf- und Sortiersysteme einen Namen gemacht hatte. NELA konnte mit TAVI.02 ein Doppelglasteller-System anbieten, das neben einer hochpräzisen Geometrieprüfung auch eine vollumfängliche Oberflächeninspektion für das bei HAGO recht breite Teilspektrum realisiert. Die Oberflächensensorik ist ausgelegt für Teile mit einem Außendurchmesser von 15- 60 mm, die Messsensorik erfasst sogar Teile mit einem Außendurchmesser bis max. 80 mm. Eine speziell für HAGO entwickelte Stanzeinzugserkennung stellt des Weiteren sicher, dass Teile mit unterschiedlichen Seiten automatisch erkannt werden und die nachfolgenden Sensoreinheiten entsprechend der jeweiligen Seitenlage angepasste Prüfbäume wählen. Eine lagerichtige Zuführung ist deshalb nicht erforderlich, was einen höheren Durchsatz zur Folge hat. Er liegt je nach Prüfteil bei bis zu 1-5 Teilen pro Sekunde. Auch kann mit der Stanzeinzugserkennung eine Vermischung spiegelverkehrter Artikel, was bei Feinstanzteilen vorkommen kann, gefunden werden.
Der Gesamtprozess der installierten Anlage umfasst die Teilezuführung, die Prüfung mit Bildverarbeitung und die Bauteilsortierung mit statistischer Fehlerauswertung. Eine Anlagenumrüstung auf ein anderes Prüfteil kann innerhalb von nur 10 Minuten erfolgen. „Die Machbarkeitsstudie und das Gesamtkonzept von NELA Brüder Neumeister haben uns überzeugt und sämtliche Systemanforderungen wurden erfüllt. Insbesondere die Möglichkeit die TAVI.02 auch im Einteller-Betrieb zu nutzen, um auch Bauteile inline zu prüfen, die aufgrund ihrer Form oder Größe nicht automatisch gewendet werden können, ermöglicht uns eine sehr hohe Flexibilität in der Produktion,“ erläutert Rainer Hack, Geschäftsführer bei der HAGO Feinwerktechnik GmbH.
Das NELA Prüf- und Sortiersystem wurde zu Beginn für 10 verschiedene Stanz- bzw. Feinschnittteile konzipiert, die Prüfanforderungen wurden gemeinsam mit dem Kunden definiert. Grenzmusterteile bildeten die Basis, um im internen Prüflabor die Konfiguration und Spezifikation der einzelnen Oberflächensensoren für eine sichere Detektion von Schlagstellen, Grat, Einkerbungen und Beschädigungen an den Bauteilkanten sicherzustellen. Die Maßhaltigkeitssensoren der dimensionalen Prüfung wurden für Reproduzierbarkeiten über den gesamten Sichtbereich von +/-10 µm ausgelegt. Das Prüfspektrum ist mittlerweile durch die Einrichtung weiterer Bauteile durch die betreuenden Mitarbeiter bei HAGO Feinwerktechnik erheblich angewachsen. Bei Bedarf bietet NELA hierbei Unterstützung an, entweder mit einem geschulten Techniker vor Ort, oder per Remote Assistance. „Damit bleiben wir flexibel und können die Qualitätsanforderungen unserer Kunden entsprechend umsetzen,“ freut sich Rainer Hack. „Die NELA-Anlage bietet uns zudem eine kontinuierliche Prüfqualität, die wir an unsere Kunden weiter geben können.“
Mit TAVI.02 konnte HAGO die automatische Oberflächenprüfung voll in die Qualitätssicherung integrieren und die Risiken der manuellen Kontrolle eliminieren. Eine Straffung der internen Abläufe, die Dokumentation und die Möglichkeit, durch Ergebnisse der statistischen Auswertung der Bauteilprüfung direkt Einfluss auf die Parameter der Produktion zu nehmen, sind deutlich verbessert worden.