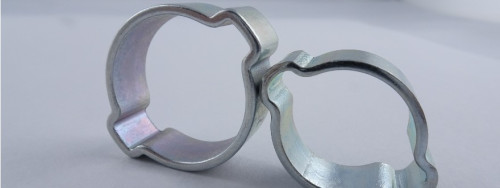
In the automotive and many other industries, in craft trade and in private households, clamps are often used for hose fittings since they are easy to handle. There are different types of clamps with different tensions, clamping forces, height and width for different requirements.
Only immaculate clamps can make sure that the clamped material isn’t damaged and that there are absolutely no leaks. Even more, clamps that are used in automated assembly processes underlie very tight tolerances as to not compromise process stability. A fully automatic optical inspection ensures that the quality level of any type of clamp is consistently high, which also constitutes an economic advantage.
Inspection requirements included a fully automatic visual control of all dimensional references of different types of clamps (ring clamps, ear clamps) with an outer diameter of up to 55mm and a height of 20mm.
The clamps are inspected by the fully automatic visual inspection system NELA TAVI.01 with integrated feeder and twin-track sorting. The system features one glass table and is equipped with sensor units tailored to the inspection task.
The DIMension sensor with a field of view of 60mm precisely captures the dimensional aspects such as width, length, width of ears, roundness, concentricity, and thickness of the clamps. Image capture is realized with a telecentric lense and telecentric backlight.
The height sensor with a field of view of 20mm precisely captures the height of the clamp above the glass table, also using a telecentric lense and telecentric backlight.
VisionCheck is the powerful image processing software developed by NELA. It processes the images captured by both sensors and combines them into one result. It then classifies each individual part as “good” or “bad”, based on pre-set parameters. The clamps are sorted accordingly. An intuitive interface allows the user to generate additional inspection profiles for similar parts.