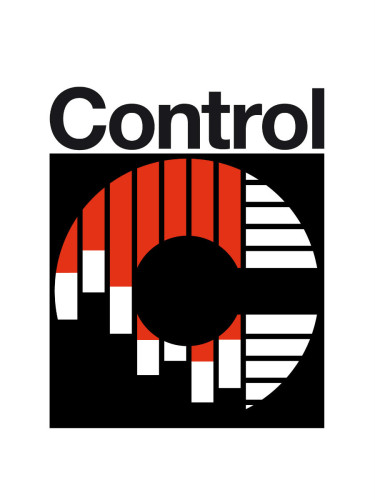
At Control 2018, NELA’s product presentation will again focus on high-precision defect inspection and geometry control of serial parts. As a specialist for fully automatic optical inspection and sorting, we will show typical applications of our versatile systems. Visitors are also invited to learn more about our new, highly precise lateral surface inspection.
Preparations for Control 2018 have been running at full speed for several weeks now as two optical inspection and sorting systems are being geared up in our show room for live operation during the trade fair. With the single glass table system TAVI.01 we will demonstrate the overall geometry control and defect inspection of formed rubber parts. For this purpose, the system will be equipped with a dimension sensor, as well as topside (for inspection of the upper surface), bottom side (for inspection of the lower surface), and in and out sensors (for inspection of the lateral surfaces). Visitors will have the opportunity to see all features and learn about the various applications for this compact inspection system directly on our booth.
When highest precision is required in defect inspection, NELA offers its proven double glass table inspection system TAVI.02. Equipped with a second rotating table, customized sensors and a flip over station, it was designed for parts which have to be inspected from both sides with equally high precision. During the fair, TAVI.02 will be showcased with dimension and height sensors (dimensional and height measurement), as well as lateral surface sensors for defect inspection on all sides of fine punched parts. – With the lateral surface sensors we can also demonstrate the “all-in-one” analysis, where all images taken by the outside sensor’s cameras of one part are put together to one image and are evaluated in one step.
NELA has added an extraordinarily interesting feature to its VisionCheck image processing software for parts that require an extremely precise surface inspection of the lateral areas. This new function is based on the pictures taken by the cameras inside the lateral surface sensor. Each of these six to twelve cameras covers a specific area of the lateral surface. The pictures overlap slightly and therefore enable the system to perform a 360° inspection of the inner and/or outer lateral part surface. Without the new feature, each picture has to be evaluated individually. With the new feature, the individual images are put together to an overall image of the lateral surface. This creates completely new opportunities for surface inspection because it is now possible to define inspection zones that are always referenced to the same reference point. Parts with slots, bore holes, notches, incisions or other characteristics are now inspected under repeatable conditions which guarantees a reliable surface inspection with highest precision and an extremely low level of pseudo waste.
Thanks to the flexibility of the NELA systems, we are able to provide an inspection solution for almost every application. Upon request, we can also offer equipment for subsequent processing, or integration with existing equipment. Customers visiting our show booth will receive a complete system presentation and comprehensive consultation from our vision inspection experts.