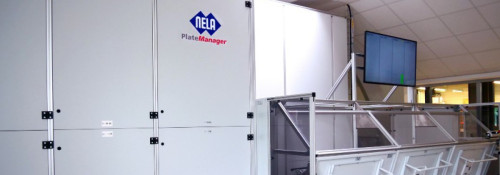
Im Zuge der Investition in eine neue 8-Farben Druckmaschine hat die französische Druckerei L’Imprimeur Simon auch die Druckvorstufe komplett automatisiert und einen NELA PlateManager installiert. Darin können bis zu 400 belichtete und gebogene Druckplatten eingelagert und kurz vor Druckbeginn abgerufen werden.
Dabei läuft die Plattenherstellung voll automatisch, eigenes Personal wird hier nur noch zum Beladen des Loaders des neuen Heidelberg Suprasetter Belichters benötigt. Um das Potenzial der beiden XL 106 von Heidelberger Druckmaschinen auszuschöpfen, musste auch die Druckvorstufe effizienter und schneller werden. Das stand für die beiden Geschäftsführer Antoine und François Simon, die den seit 1909 bestehenden Familienbetrieb in der Nähe von Besançon leiten, von Anfang an fest. In der Branche hat sich L’Imprimeur Simon als Experte für den Druck hochwertiger Fotobücher und Magazine einen Namen gemacht.
Über Heidelberg France kam der Kontakt zu NELA zustande, es wurde aber zunächst über die Inline-Abkantung der Druckplatten sowohl für eine ältere XL 106 / 4 als auch für die neue XL 106 / 8 gesprochen. Schnell stellte sich jedoch heraus, dass es im rund um die Uhr laufenden Druckbetrieb immer wieder zu Verzögerungen kam, wenn aufgrund von Änderungen im Produktionsplan Plattensätze manuell umsortiert werden mussten. Dabei kam es immer wieder vor, dass Druckplatten verkratzt oder anderweitig beschädigt und daher erneut belichtet werden mussten. Da immer Plattensätze für mehrere Druckaufträge vorgehalten wurden, war das Sortieren ein aufwändiger und zeitraubender manueller Prozess, der auf jeden Fall eliminiert werden sollte.
Im Projektgespräch mit NELA fand sich schnell eine Lösung: der NELA PlateManager. Ein Besuch bei Krüger Druck im saarländischen Merzig, wo seit 2020 eine solche Anlage in Betrieb ist, überzeugte die beiden Geschäftsführer von L’Imprimeur Simon. Der PlateManager dient als intelligenter Plattenspeicher, in welchem belichtete und gebogene – also druckfertige – Offsetplatten eingelagert werden. Jede Platte erhält ihr eigenes Fach, so wird sie weder verkratzt noch beschädigt. Identifiziert werden die Platten über einen aufbelichteten Datamatrix-Code, der vor Einlagerung in den PlateManager gescannt wird. So weiß der Speicher immer, welche Druckplatte sich in welchem Ablagefach befindet und zu welchem Druckauftrag sie gehört. Am Terminal des PlateManager wird angezeigt, welche Plattensätze für welche Druckaufträge gerade eingelagert und vollständig sind, bzw. wo noch Druckplatten fehlen. Da der Inhalt des Datamatrix-Codes als Klartext auf die Rückseite jeder Platte aufgedruckt wird, kann der Bediener sie auch ohne digitale Anzeige jederzeit zuordnen.
Der nächste Plattensatz kann entweder direkt am PlateManager abgerufen werden, oder an einem Terminal, das zwischen den beiden Druckmaschinen-Leitständen positioniert ist. Die entsprechenden Druckplatten werden dann in der von der Druckmaschine vorgegebenen Reihenfolge aus den Slots entnommen und außerhalb des PlateManagers in einen Plattenstapler mit Trolleys abgelegt. Dieser Stapler wurde auf Wunsch des Kunden so konzipiert, dass die Druckplatten vertikal, d.h. mit der Abkantung zur Seite, abgelegt werden. Zwischen den Plattensätzen ist jeweils ein Versatz, dadurch können die Plattensätze vom Drucker leichter entnommen werden. Außerdem vergrößert sich durch die vertikale Abstapelung die Kapazität des Trolleys, d.h. er kann bis zu 72 Druckplatten aufnehmen.
Der PlateManager brachte eine völlig neue Flexibilität in die Produktion bei L’Imprimeur Simon, da kurzfristige Änderungen im Produktionsplan jetzt keine manuelle Sortierarbeit mehr verursachen. Es wird dann eben einfach – innerhalb von nur drei Minuten – ein anderer Plattensatz ausgelagert und im Trolley an die Druckmaschine gebracht.
Antoine und François Simon sind begeistert von ihrer neuen Druckvorstufe: „Wir benötigen heute kein Personal mehr für die Belichtung und Bereitstellung der Druckplatten. Die Drucker rufen den nächsten Druckauftrag ab und holen sich die Plattentrolleys am Stapler. Wir können wir die Druckplatten für die komplette Produktion auf beiden Druckmaschinen vorproduzieren.“
Der PlateManager wurde von NELA mit 400 Plätzen konzipiert, so dass die Rund-um-die-Uhr-Produktion versorgt ist. „Die Speicherkapazität des PlateManagers wird immer auf den Bedarf des Kunden angepasst,“ so Projektleiter Hubert Boxberger von NELA. „Das Maschinenkonzept ist flexibel und ermöglicht unterschiedliche Wege der Anbindung und Sortierung.“
Für L’Imprimeur Simon hat sich die Investition heute schon gelohnt. „Das System ist bedienerfreundlich und zuverlässig und führt zu deutlich verbesserten Arbeitsbedingungen für unserer Drucker, die die Druckplatten heute nur noch zum Einhängen in die Druckmaschine anfassen müssen. Und die neu hinzu gewonnene Flexibilität in der Produktion können wir direkt an unsere Kunden weitergeben!“
Unser oberstes Ziel war es, die manuelle Sortierung der belichteten Druckplatten abzuschaffen. Für unsere 24-Stunden Produktion mit unterschiedlich langen Läufen ist es wichtig, dass die Druckplatten für die nächsten Jobs fertig sind und schon in der richtigen Reihenfolge für die Druckmaschine bereitstehen. Wir wollten über diesen Arbeitsschritt überhaupt nicht mehr nachdenken müssen. Mit dem PlateManager haben wir eine Möglichkeit gefunden, immer Platten für mehrere Jobs vorrätig zu haben. Und wir können flexibel entscheiden, welcher Job als nächstes dran ist.
Alle Abläufe, die mit der Bereitstellung der Druckplatten zusammenhängen, sind viel schneller und reibungsloser geworden. Unsere Drucker können völlig autonom die Platten abrufen, es gibt weniger Reibungspunkte mit der Vorstufe. Jede Platte wird nur noch einmal angefasst, und zwar beim Einhängen. Auch hier gewinnen wir Zeit, die Arbeitsabläufe sind für unser Personal einfacher und komfortabler. Insgesamt hat sich der Arbeitsaufwand in der Druckvorbereitung um 25% reduziert, so dass wir einen Mitarbeiter komplett mit anderen Aufgaben betrauen konnten.